LiuGong News
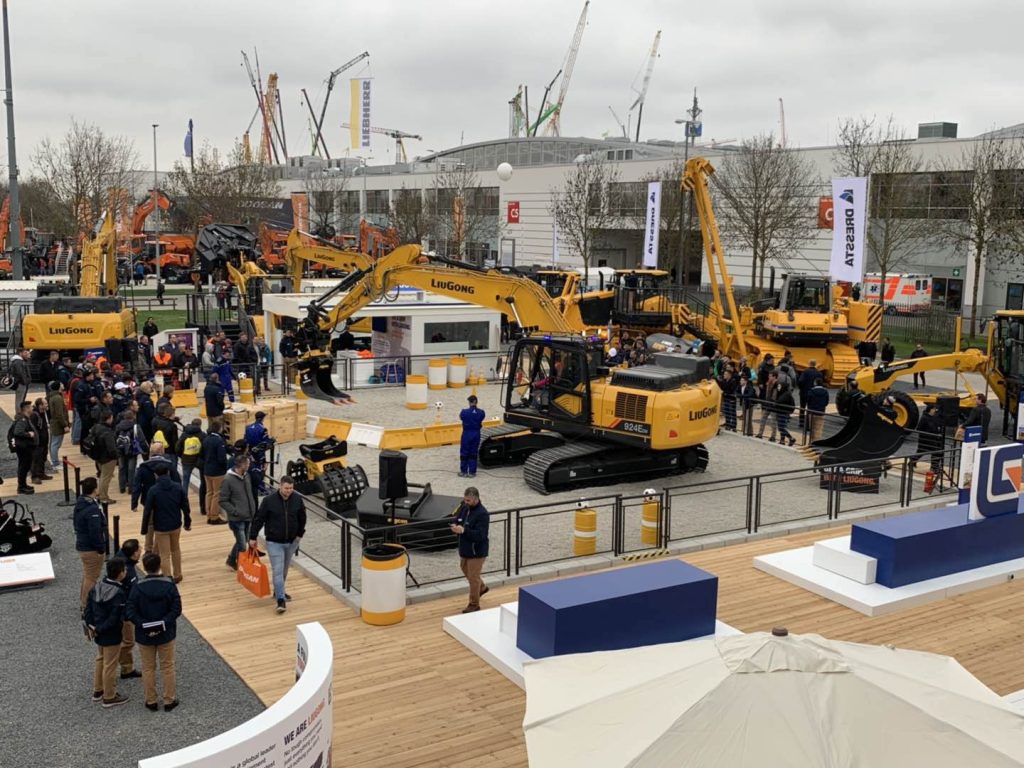
bauma represents a unique opportunity for manufacturers to showcase their full line of products and services to a global audience. Predictably, in this highly charged exhibition environment, “shouting the loudest” has become the primary communications method. However, LiuGong and Dressta aim to take a radically different approach to bauma in 2019.
LiuGong and Dressta’s approach is focussed on creating a booth where customer feedback, dialogue and collaboration take centre stage. They will showcase a twenty machine line up of tough equipment designed for the world’s toughest conditions. This line-up clearly demonstrates the company’s capability to deliver machines for every major application; mining, quarry and aggregate, demolition, material handling, utilities, landscaping, road and highway and agriculture. Nine new models will be making their bauma debut and have been inspired by close collaboration with customers. They include new; wheel loaders, excavators, the Red Dot Award winning motor grader, a forklift and two new dozers from Dressta. “Our design DNA,” commented Gary Major, Director of Industrial Design, “is genuinely driven by the voice of the customer. I believe customers and visitors at bauma will recognise their input and I’m keen to hear and see their reactions to our new LiuGong and Dressta machines.”
Instead of applying the usual marketing argumentation to the booth, LiuGong and Dressta’s principal communication aim is to generate real customer feedback for their products and services – live. According to Chairman of LiuGong Europe and Dressta, Howard Dale, “Nothing is off limits. We genuinely want to know what customers like, what they don’t like and where they see the gaps in the market for products and services.” The company’s approach is to take its bauma booth beyond a sales and corporate platform and create a valuable learning experience. Dale explains, “As a company, we try to be extremely close to customers. In our day-to-day work we run customer clinics and dialogues, which are immensely valuable to our design process. We have a strong ambition to go “beyond equipment” but, if we just use bauma to talk about today’s products and services, then we have missed a massive opportunity. Where else,” he asks,” can you hope to find such a diverse and knowledgeable audience in one location?”
LiuGong and Dressta’s plan for bauma is ambitious, so what can we expect from the exhibition booth?
The nerve centre of the booth will be an interactive “Listening Lab” where guests can freely post their thoughts on some big industry trends. The interaction carries on to the new model display machines too. Each of these new machines will feature demos hosted by designers, engineers and customers, broadcast live across the booth and live on social media. There will also be a listening corner where visitors will be asked to give input on the next generation wheel loader project. “There is a story of customer collaboration behind the development of every one of our machines,” said Dale, “our message is that we are listening, and we are committed to working with customers to make their business better.”
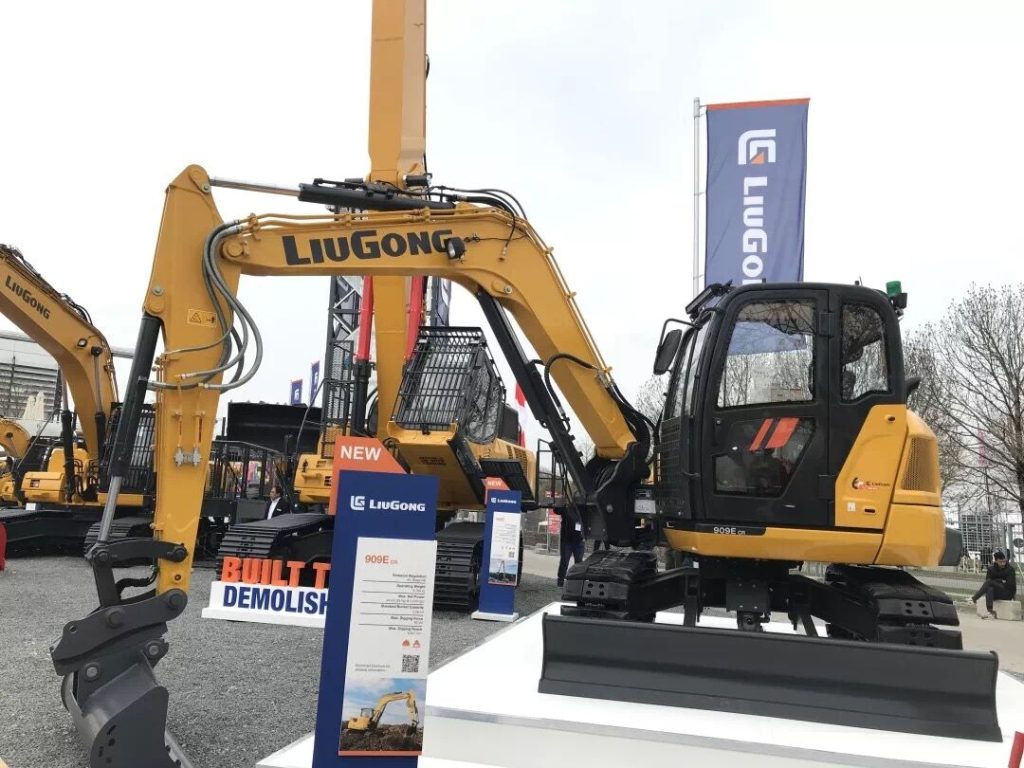
The new 909ECR excavator is a perfect example of this customer centric-approach. “Our UK plant hire customers asked us for a compact radius machine which would fill the gap in their rapidly growing market. The desire for greater operational stability and an improved tool handling capability were consistently voiced by our customer panels and in operator feedback sessions,” confirmed Dale. “With the new 909ECR we’ve proved that we’ve listened, acted and delivered.” The LiuGong Development Process (LDP) which involves customers at every stage has created a machine which is tailored for the plant hire segment and will excel in inner-city and road applications.
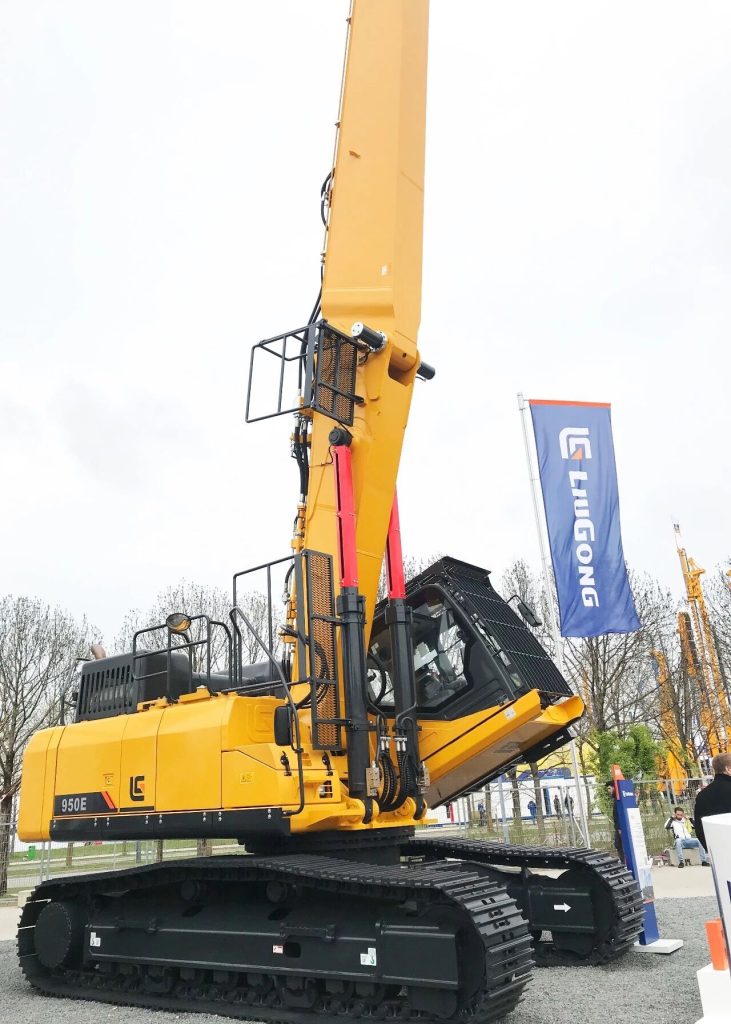
Significant highlights in LiuGong’s offering also includes the new 950E high-reach heavy demolition excavator . Extensive customer consultation and close collaboration with partners such as Kocurek UK, have resulted in a machine which, in Dale’s opinion, “the demolition industry would design for itself.” The fact that a growing number of customers have already placed repeat orders further underlines this belief. Positive customer feedback focuses on the machine’s improved stability and stronger 30m boom which allows the 950E to punch well above its weight. Greater break-out force and the ability to handle heavy weight attachments ensures that the 950E gets the job done faster.
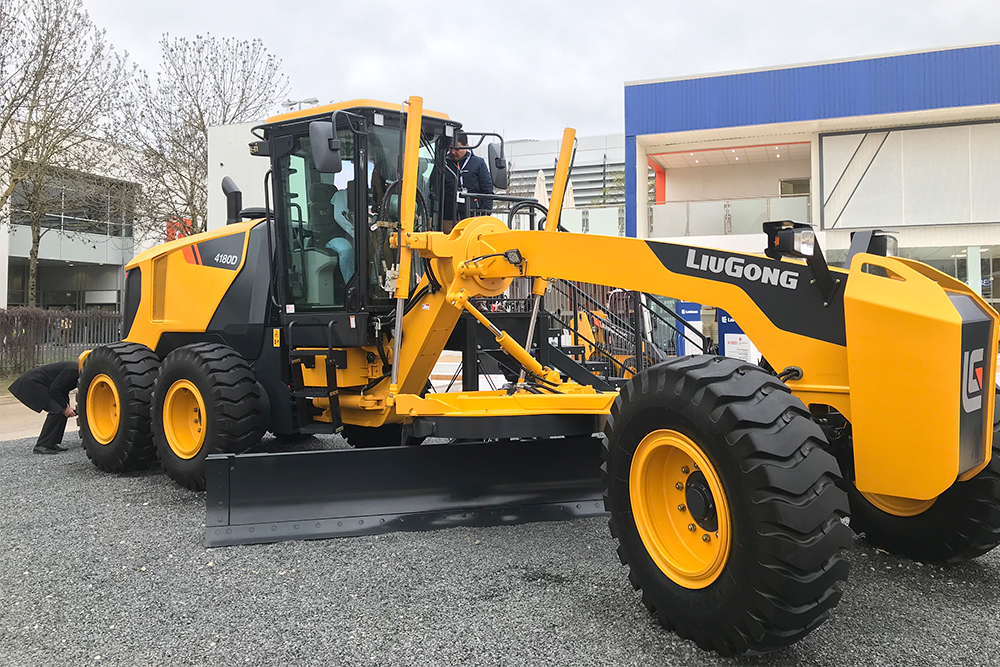
Also making its debut is the new, Red Dot Award-winning 4180D motor grader. A completely new machine the 4180D is the embodiment of LiuGong’s design DNA. The UK based design team worked in close co-operation with customers and operators to rethink the traditional grader. According to Major, “visibility, operator comfort and ergonomics were quickly identified as the key areas of focus along with tool articulation and maneuverability.” The resulting machine boasts 324° panoramic visibility owing to a newly designed 5 post cab with a single C-pillar, a completely new cab interior which sets the benchmark for comfort and efficiency. New impact-resistant materials have also been introduced to provide better weight distribution and increased recyclability. In addition, access for routine maintenance has also been improved to reduce downtime.
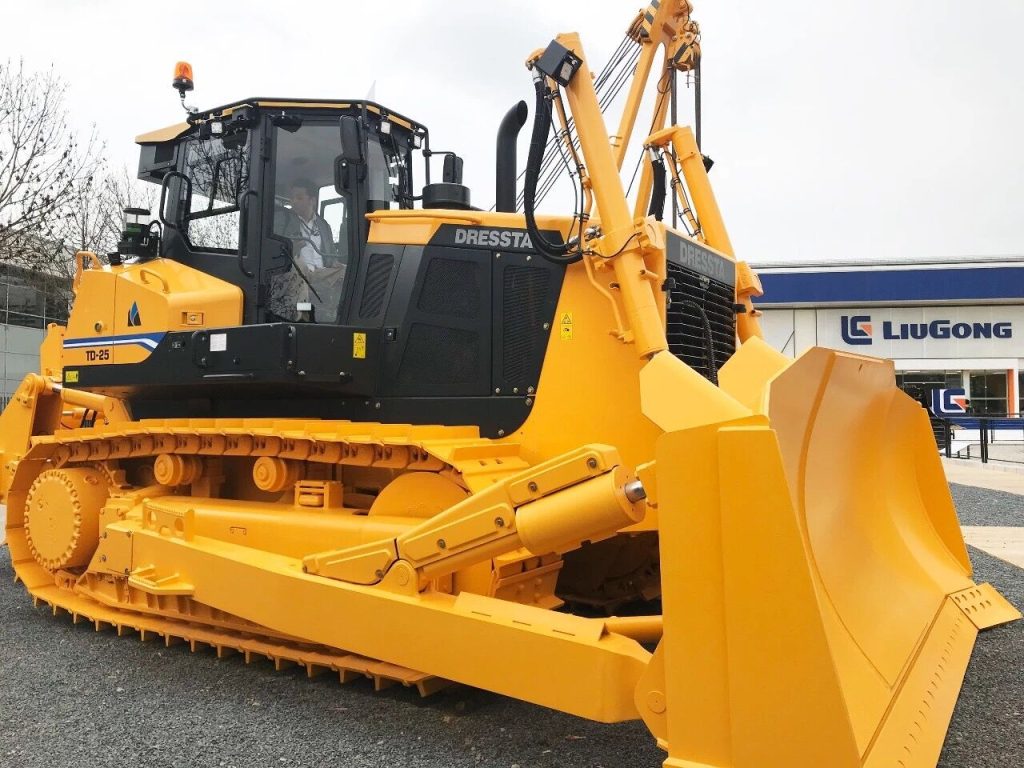
For Dressta, customer collaboration is also engrained in the company’s product DNA. The new TD25 crawler dozer is a perfect example of listening in action. The UK industrial design team conducted exhaustive customer research into the operator’s world before designing the new TD25. Visibility, comfort and safety were highlighted as key focus areas. “The operator feedback was invaluable in helping us reassess the crawler dozer as a working tool,” remarked Major. Visibility and safety have been greatly improved with 30% more glass in the cab and the inclusion of rear cameras. The operator environment has been radically improved within the pressurized cab. Special attention has been focused on the operational ergonomics to improve ergonomics and reduce operator fatigue. Improvements in the suspension and hydraulics further improve the operator experience by reducing noise and vibration.
Some commentators might see LiuGong and Dressta’s communication approach at bauma as high risk, after all, in this highly stage-managed arena, they are effectively opening themselves up to criticism. Dale, however, is bullish “There is a lot of marketing hype at events like bauma, with manufacturers making claims and counter claims about what their products will do. I think we, as a company, have moved on from all of that. Our business is pretty simple – it’s about giving customers what they really need. Open dialogue is absolutely crucial to this so I’m looking forward to getting those conversations started and see where they take us.”